Grand Isle Shipyard recovers $100,000 in stolen assets with Asset Tag
With Samsara, Grand Isle Shipyard has transformed their operations, improving processes like vehicle maintenance and asset tracking. The visibility they gained with Samsara enables their proactive approach to safety and improves accountability across the organization.
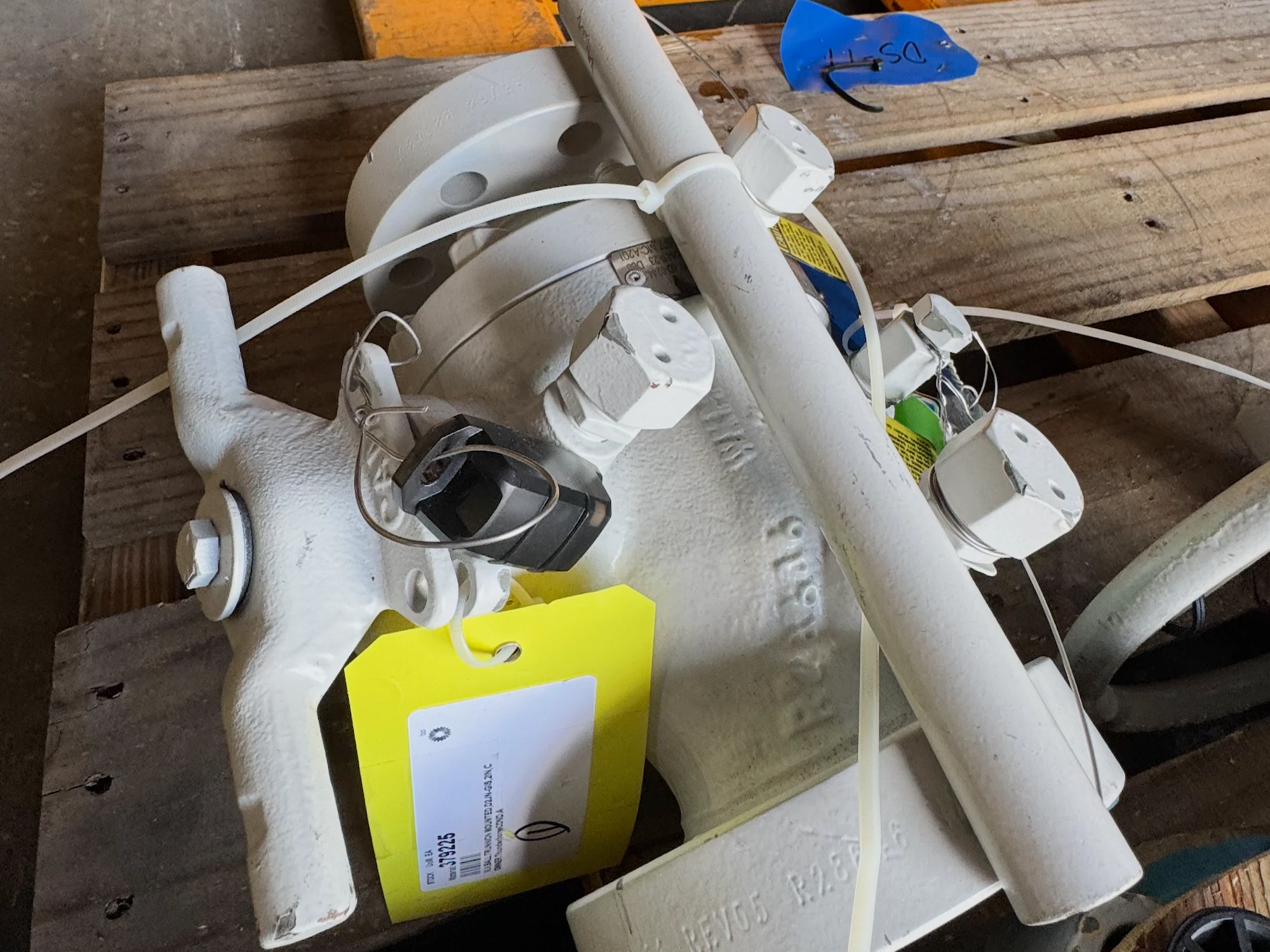
Powered by the Samsara Connected Operations Platform
Meet Grand Isle Shipyard
Grand Isle Shipyard needed to free up their back office from tedious reporting
Grand Isle Shipyard (GIS) has over 75 years of experience providing infrastructure, electrical and instrumentation, and maintenance services to the oil and energy industry. To deliver the best possible service to their customers, they equip their mobile workforce with cutting-edge technology to ensure productivity and efficiency, as well as constant connectivity with the back office.
However, their previous telematics system was difficult to pull data from, taking up to four days to find the necessary information. This impacted the back office when working towards deadlines on critical work streams like payroll and fuel management. Additionally, without visibility into their vehicles or equipment, it was difficult to determine how damage occurred and exonerate drivers when they were involved in incidents.
DEREK CHAMPAGNE
An integrated platform enhanced with AI
Samsara’s suite of workforce, asset, and fleet management solutions made the decision to go with Samsara simple for GIS—rolling out Asset Tags, AI Dash Cams, Connected Workflows, Asset Gateways, and Vehicle Gateways across their operations. The platform's ability to consolidate vehicle, equipment, and personnel data in one place provided GIS with the granular visibility they were looking for. Additionally, Samsara's AI Dash Cams aligned with GIS's existing use of AI, making them a natural fit for their operations.
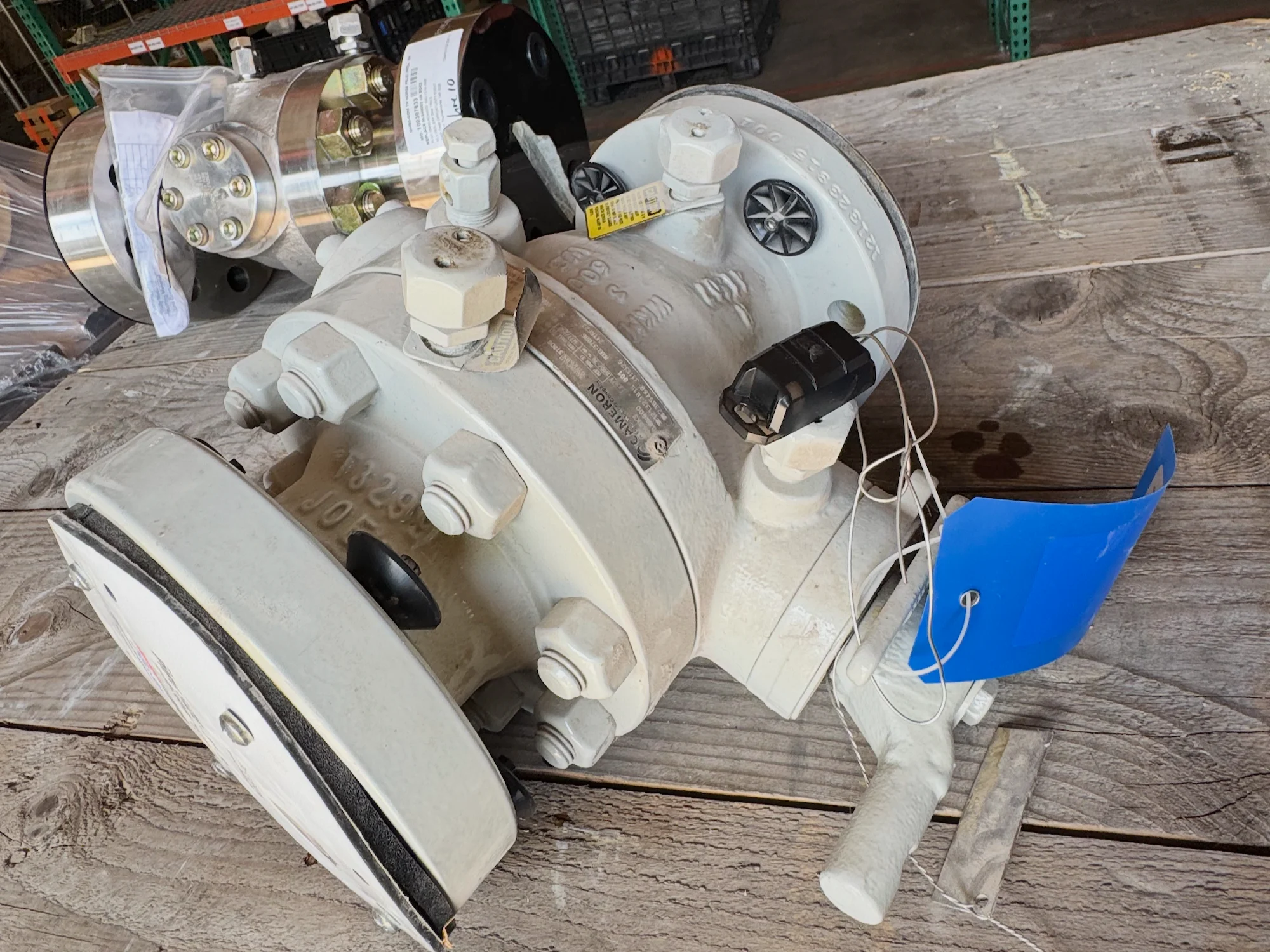

Reducing time spent on vehicle inspections by 83%
Before Samsara, GIS’ monthly vehicle inspection process consisted of two steps: first, drivers completed the paper or Excel form, followed by emailing vehicle photos in. This led to forms not getting completed or going missing, causing vehicle issues to add up. By digitizing this process with Samsara Connected Workflows, GIS reduced how long it takes to complete vehicle inspections by 83%—and drivers can do everything, including photo submission, in the Driver App. Now, work orders are triggered every time an issue is logged, enabling easy follow through and fast repairs.
LEARN HOWERIC CARLSON
Decreasing at-fault accidents by 50% and distracted driving by 99%
Before Samsara, GIS had limited visibility into their vehicles which meant damage often went unreported and exonerating drivers was a challenge. With vehicles costing up to $90,000, they installed Samsara AI Dash Cams to protect their fleet and team. Since turning on in-cab alerts, driver behavior has significantly improved—notably, GIS reduced distracted driving by 99% and no seatbelt use by 91%. The combination of improved safety habits and HD footage has enabled GIS to reduce at-fault accidents by 50% and avoid costly litigation.
LEARN HOW

Fast payroll processing and better fuel spend control with GPS data
GIS’ mobile workforce submits weekly timesheets but their previous telematics system made payroll verification a challenge. With instant access to GPS data in the Samsara dashboard, GIS can quickly and accurately verify hours worked and efficiently process payroll. Additionally, Samsara’s accurate location tracking helps identify fuel discrepancies, reducing unauthorized fuel use and improving overall cost control.
LEARN HOW