How Dohrn took a unified approach to maximizing their fleet operations
By leveraging the Samsara Connected Operations™ Cloud to unify data across trailer and vehicle telematics, sites, and driver safety, Dohrn Transfer Company has transformed the efficiency and safety of their operations.

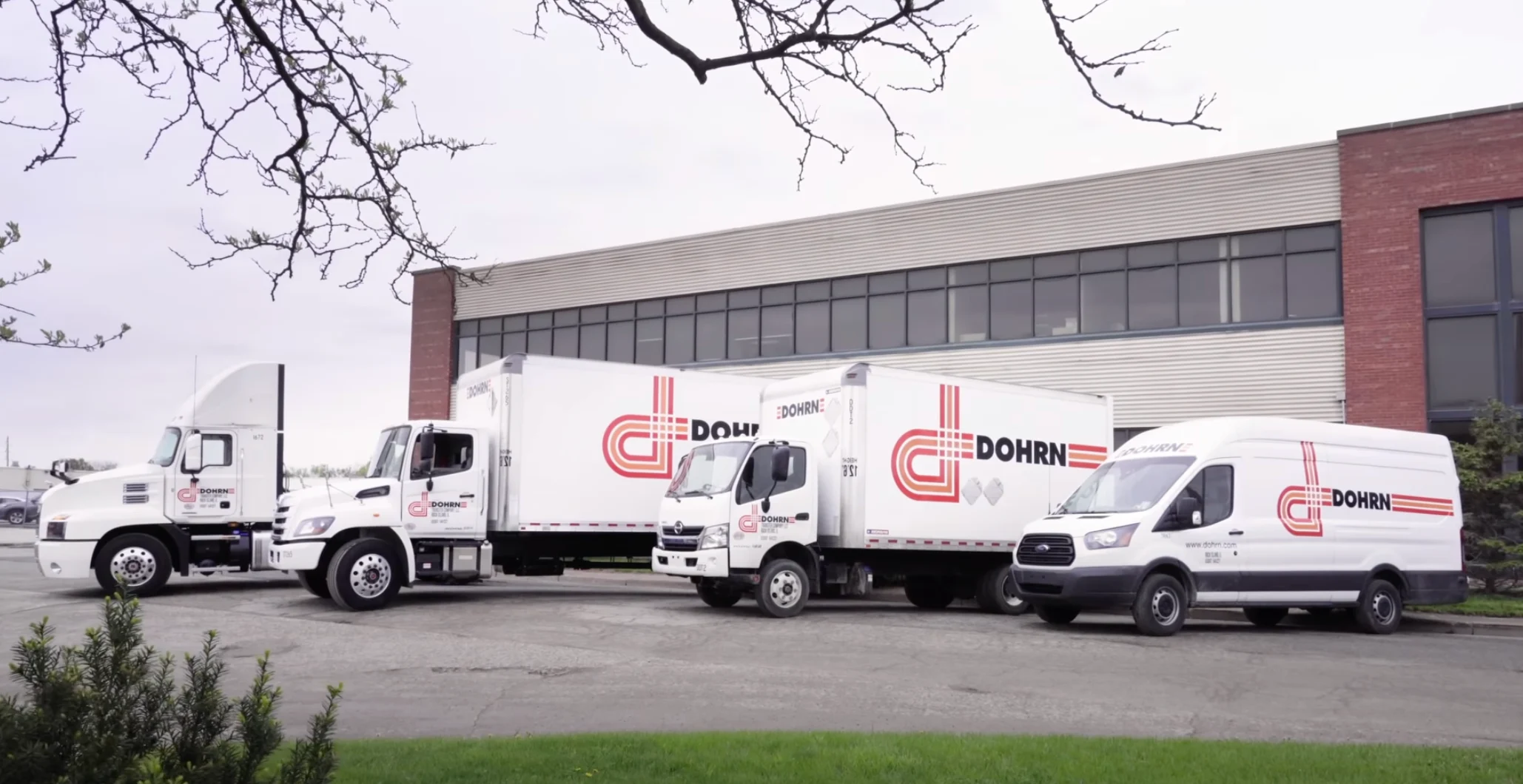
Watch Video
Unifying data with an all-in-one platform
Meet Dohrn Transfer Company
Dohrn Transfer Company needed to unify their data to improve safety and operational efficiency across their organization.
Dohrn Transfer Company is a less-than-truckload carrier that provides trucking services and local delivery across the United States. After over a century of best-in-class service, they needed to find a solution for ELD compliance to meet hours of service regulations.
Initially, Dohrn was looking for a modern and driver-friendly solution to ensure their fleet of over 600 assets remained compliant as they operated across 14 states and 22 terminals. But as the Dohrn team began to evaluate various providers, they realized that they had needs far beyond just ELD compliance.
Dohrn sought an integrated solution that could connect their data and consolidate their fleet operations in a single pane of glass. In addition to ELD compliance, Dohrn also saw an opportunity to leverage real-time data to improve operations such as trailer management, chain of custody, dispatch, maintenance diagnostics, fuel usage, and driver safety.
J.D. BARNES
Unified platform improves operational efficiency
With the Samsara Connected Operations Cloud, Dohrn has found three of their most important criteria for technology—real-time visibility, ease-of-use, and employee engagement. By unifying their operations within a single integrated platform, Dohrn is able to improve operational efficiency, boost driver retention, and reduce costs.

Smarter trailer operations with real-time visibility
With demand for trailers at an all-time high, Dohrn needed a way to protect their assets and maximize their utilization. Previously, Dohrn’s trailer operations were manual and paper-based, which led to inefficiencies in trailer management and time-consuming yard hunts to recover trailers.
With Samsara, Dohrn now has complete visibility into the location and utilization of their trailers. By leveraging real-time data, Dohrn now knows exactly where their trailers are and can quickly retrieve them to get them back into service for their customers—saving an estimated $75,000 per year in lost revenue.
LEARN MOREComplete visibility into the chain of custody
Dohrn needed a better way to protect their sites and track the location of their assets. By deploying a combination of Site Visibility and Trailer Tracking, Dohrn now has complete visibility into the chain of custody of their assets.
For example, Dohrn used Site Visibility to identify where a trailer was loaded by quickly retrieving video footage. Then, Dohrn leveraged Samsara’s real-time data from their trailers to find the freight. As a result, Dohrn estimates they are saving $20,000 per year in loss claims.
Learn more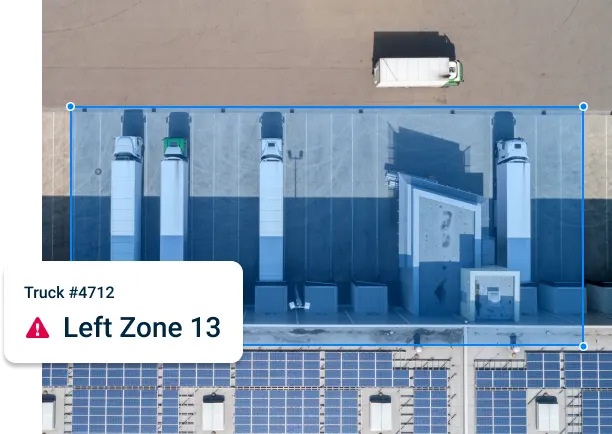

Real-time visibility improves fleet performance
With Samsara deployed across all 500+ of their vehicles, Dohrn now has real-time visibility into the location and performance of their vehicles. Real-time GPS data has streamlined dispatch and improved driver productivity, reducing idling by 50%. Dohrn is also using DVIRs to proactively reduce vehicle downtime, accelerating response times to maintenance issues by 40%.
LEARN MOREA comprehensive safety program reduces incidents and improves retention
With Samsara’s video-based safety solution, Dohrn has transformed their safety program by taking a proactive approach to driver coaching—decreasing harsh driving events by 88%.
Dohrn also started a new safety award program, introducing gamification into driver safety by leveraging Samsara Safety Scores. As a result, Dohrn was able to reduce driver turnover by 10%, saving $8,000 in recruitment and replacement costs per driver.
LEARN MORE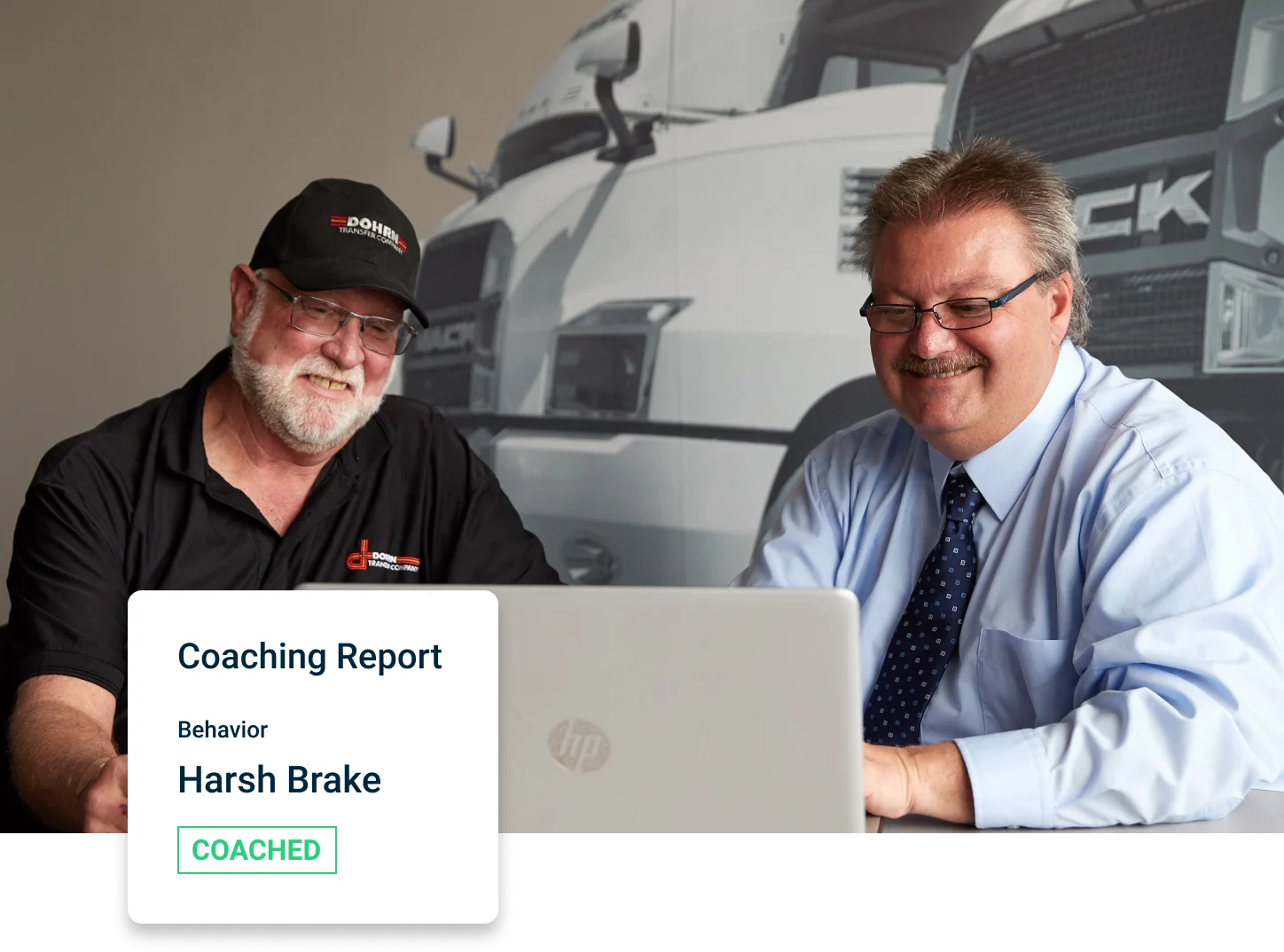

Improving operational efficiency with Samsara’s open API
Dohrn leverages Samsara’s open API to streamline manual processes such as tax auditing, dispatch, and data analytics.
In one example, Dohrn integrated Samsara trailer and geofence data with their business intelligence system to improve efficiency and reduce administrative workload, saving approximately 780 hours per year on manual billing for a single client.
LEARN MORE