DeSilva Gates Protects and Optimizes Their $200M Equipment Fleet with Samsara
With Samsara Connected Workflows, Asset Tag, and more, DeSilva Gates effectively protects their fleet and optimizes their workflows.
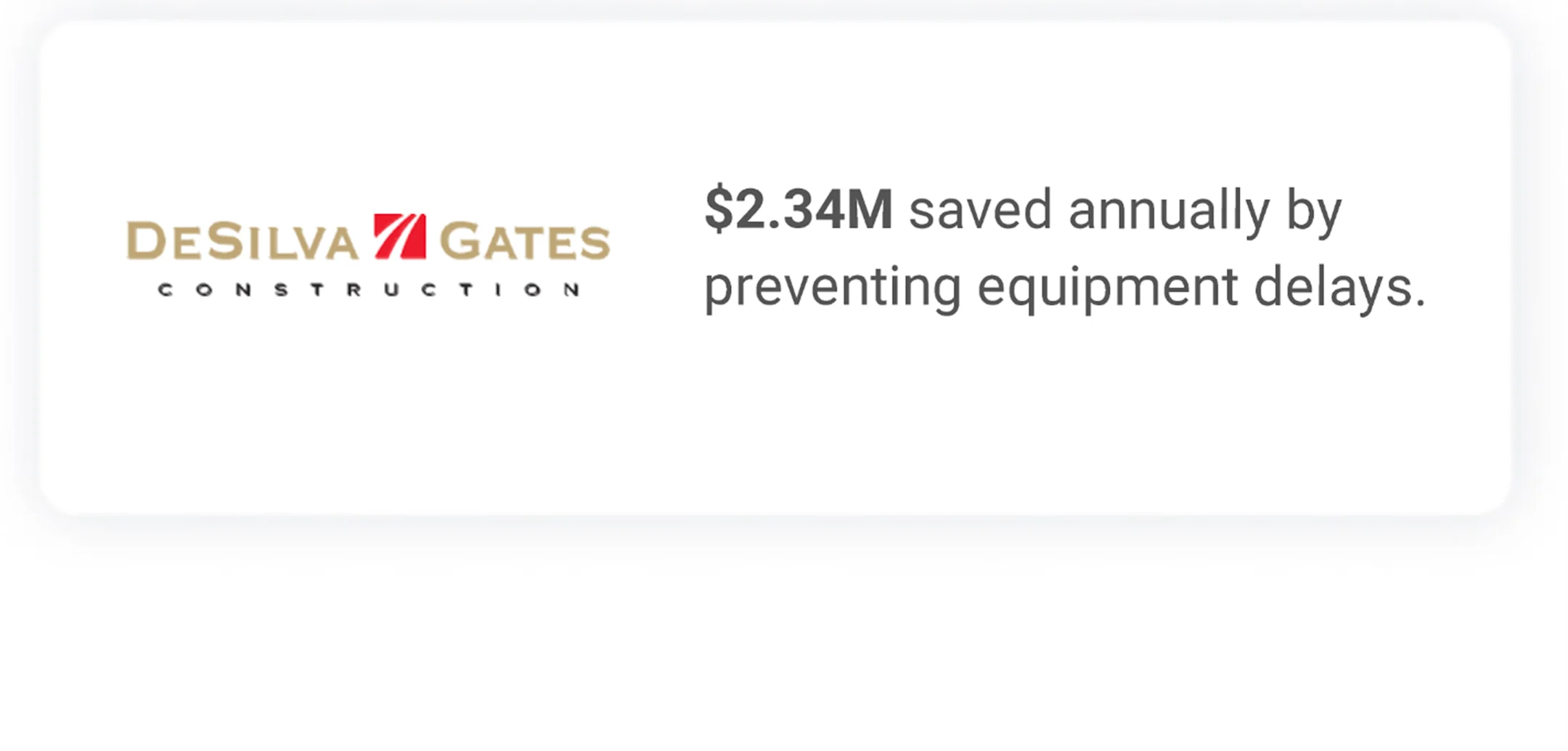
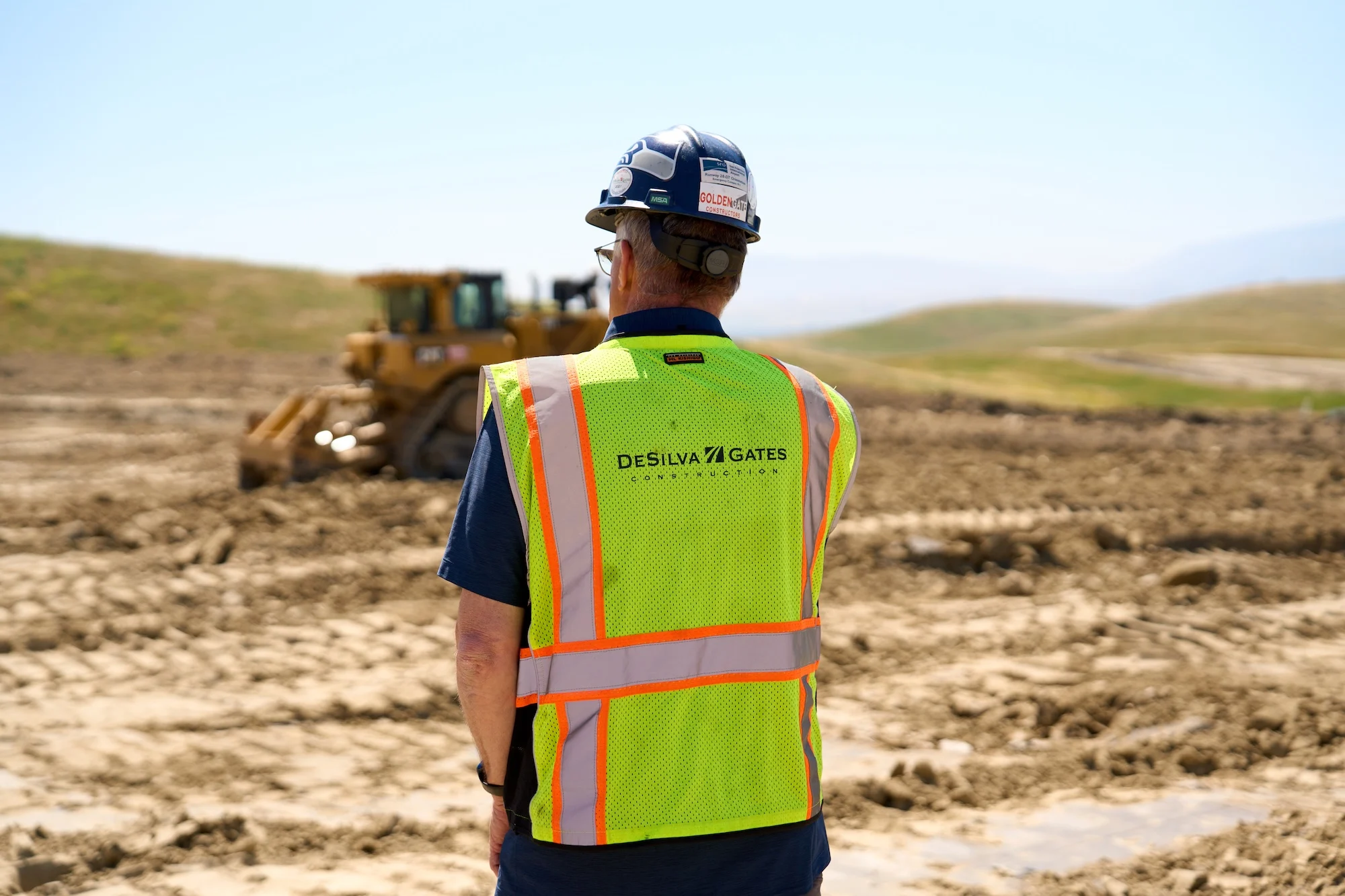
Powered by the Samsara Connected Operations Cloud
Meet DeSilva Gates Construction
Inefficient systems were costly and left DeSilva Gates vulnerable to theft
DeSilva Gates Construction, a Bay Area-based company established in 1932, provides clients with a wide range of services including demolition, excavation, trucking, earthwork, and hazardous materials removal. DeSilva Gates faced several critical challenges that hindered its operational efficiency and financial performance. Due to manual tracking of equipment and paper-based processes, DeSilva Gates experienced significant inefficiencies and delays, making it difficult to address issues promptly. Limited visibility into the location of their equipment led to high risk of equipment theft, compromising their ability to recover stolen assets. Additionally, inaccurate billing and extensive administrative work meant costly inefficiencies and increased labor costs. These challenges collectively impacted DeSilva Gate’s safety protocols, operational accountability, and overall bottom line.
RICH POPPOFF
Automated tracking and real-time monitoring transform DeSilva Gates Construction
With Samsara, DeSilva Gates has seen improved efficiency, significant cost savings, enhanced safety, and better accountability across its operations. The ability to quickly address issues and provide clear evidence in case of incidents has made a substantial positive impact on the company's bottom line and operational effectiveness.
Saving $2.34M annually by preventing job delays caused by paperwork inefficiencies.
Previously, incomplete maintenance checks meant that faulty equipment was often delivered to job sites, causing significant delays. With Connected Workflows, these issues are reported and addressed immediately, ensuring jobs start on time. As a result of preventing equipment delays, DeSilva Gates saves an estimated $45,000 a week, translating to approximately $2.34 million saved annually.
LEARN MORE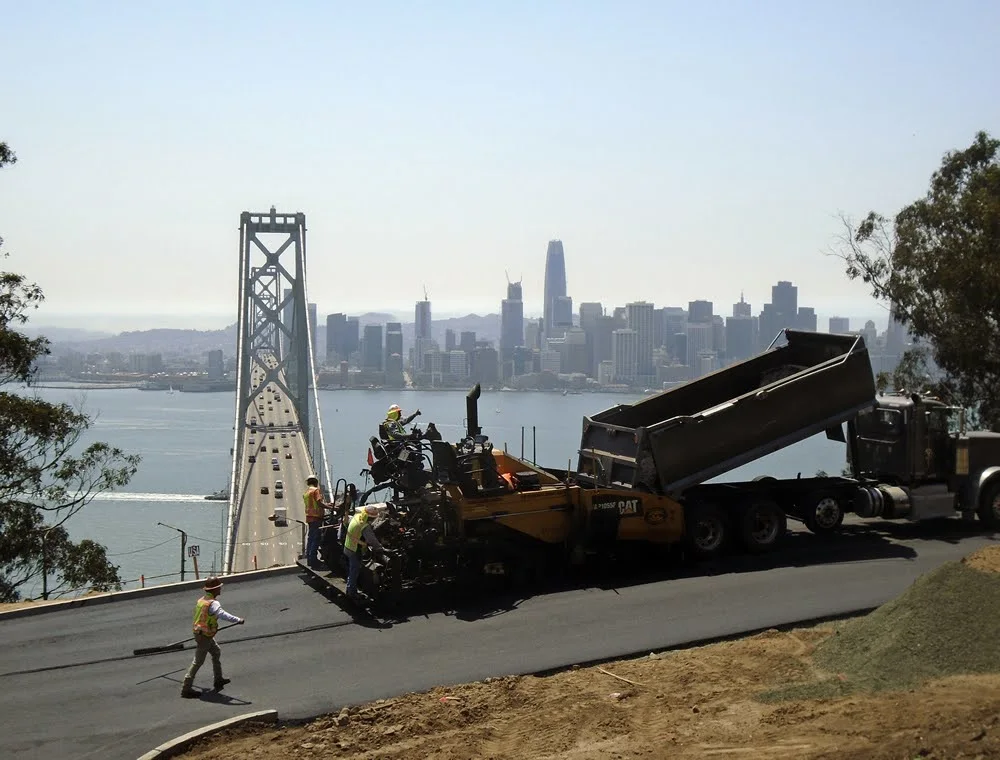
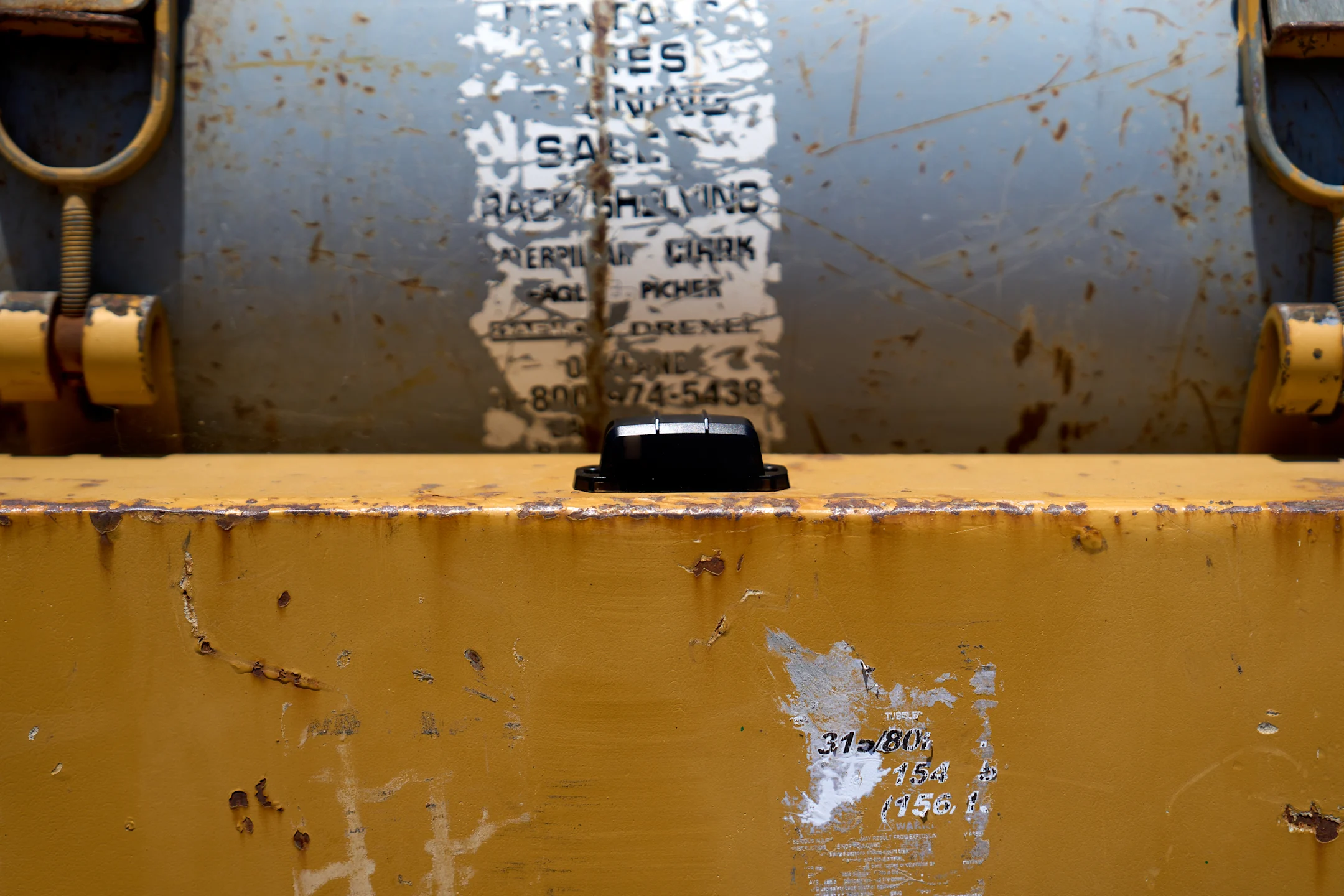
Protecting a $200M equipment fleet from theft.
DeSilva Gates has an expansive fleet of over 350 pieces of heavy construction equipment, valued at $200 million. Asset Tag helps DeSilva Gates add a layer of protection to their most high-value assets and provides comprehensive tracking of smaller, previously untracked equipment. The enhanced tracking capabilities not only deter theft but also improve inventory management, ultimately boosting operational efficiency.
LEARN MOREEnsuring accurate billing and saving $60,000 annually.
By tracking the exact hours of their rented equipment usage with Samsara Asset Gateways, DeSilva Gates ensures that billing reflects actual usage instead of relying on estimates or manual reports. This precision removes discrepancies and prevents fraudulent entries, ensuring clients are billed correctly and transparently. Additionally, the automated tracking reduced the need for administrative work, eliminating annual labor costs of $60,000.
LEARN MORE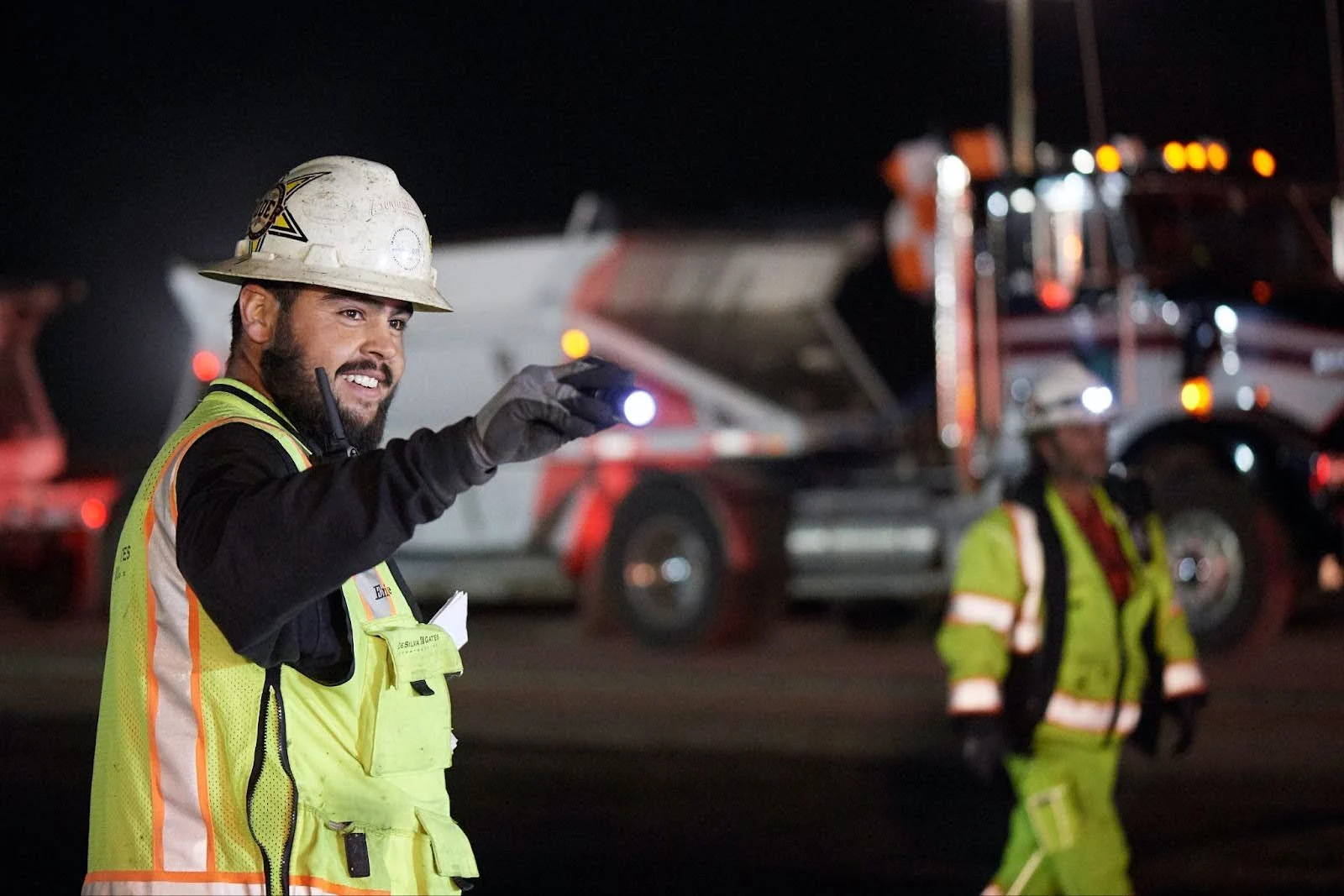
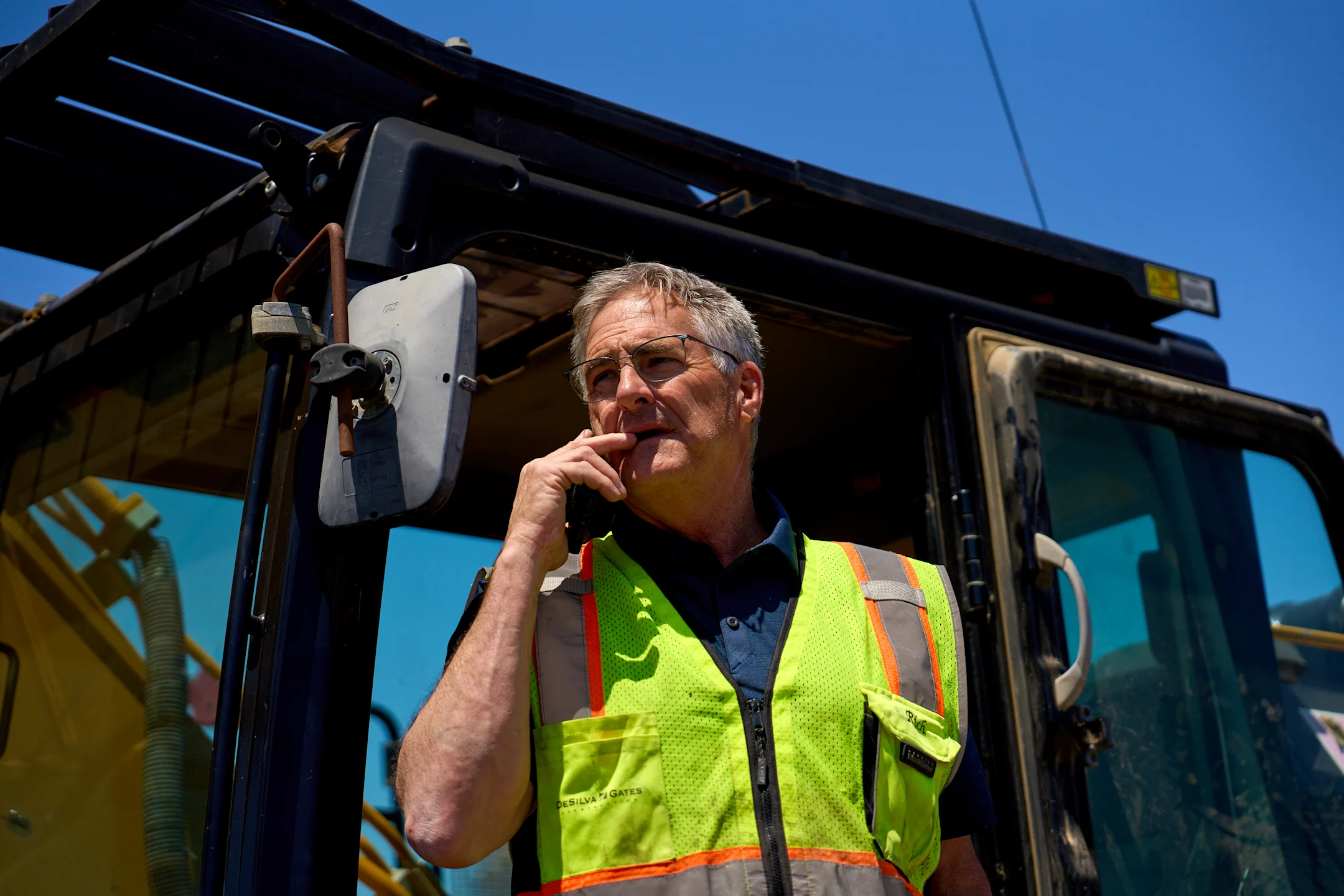

Overturning 90% of insurance claims with Samsara AI Dash Cams.
Samsara AI Dash Cams provide DeSilva Gates with a powerful tool to improve safety, protect and exonerate drivers, and achieve substantial cost savings—allowing them to enhance their coaching and safety program. As a result, DeSilva Gates estimates they’ve been able to reverse 90% of insurance claims against the company with dash cam footage.
LEARN MORE