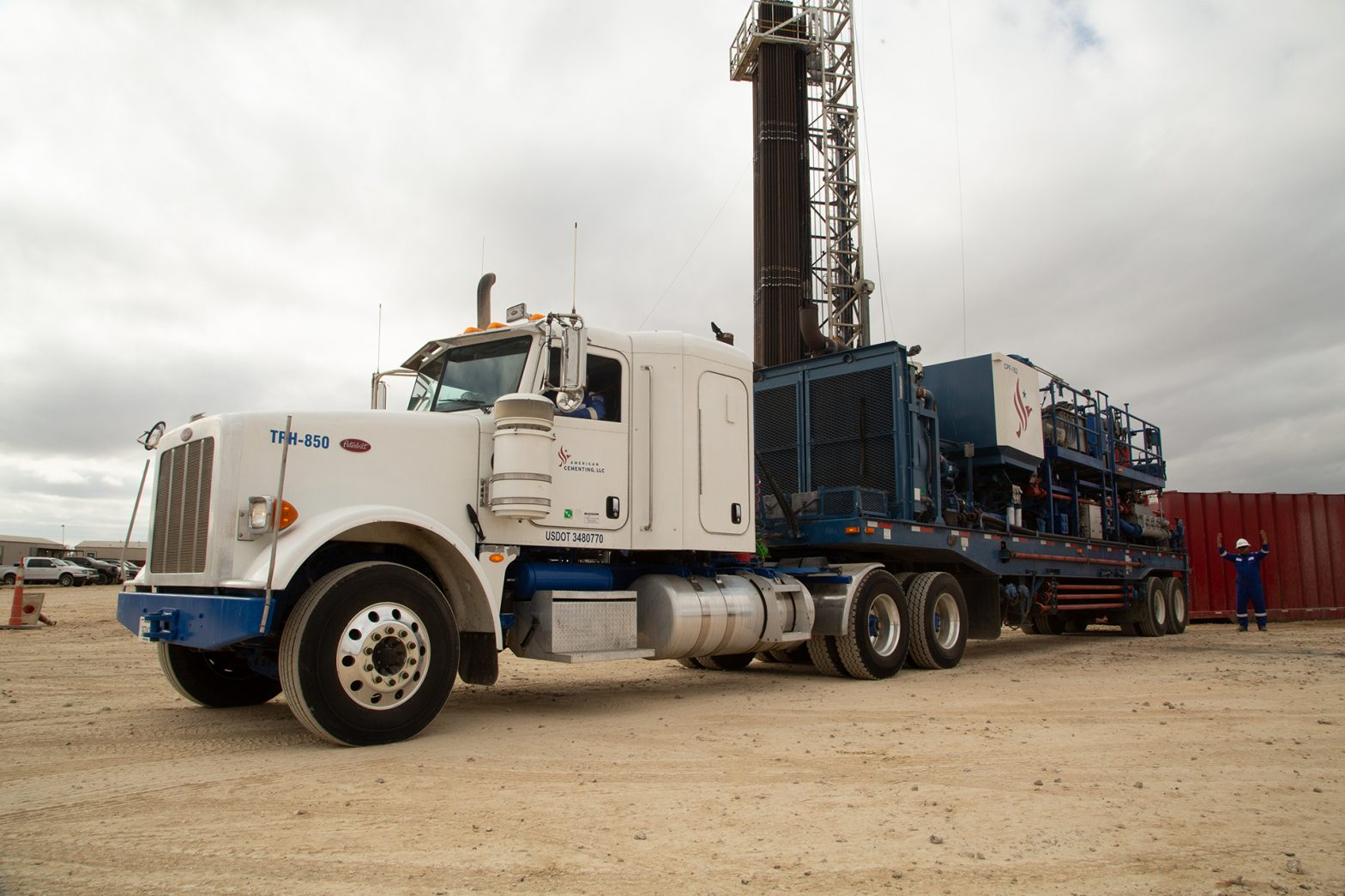
How American Cementing Went Paperless and Connected Their Operations to Improve Efficiency
With Samsara, American Cementing improved efficiency for both field technicians and the back-office team.
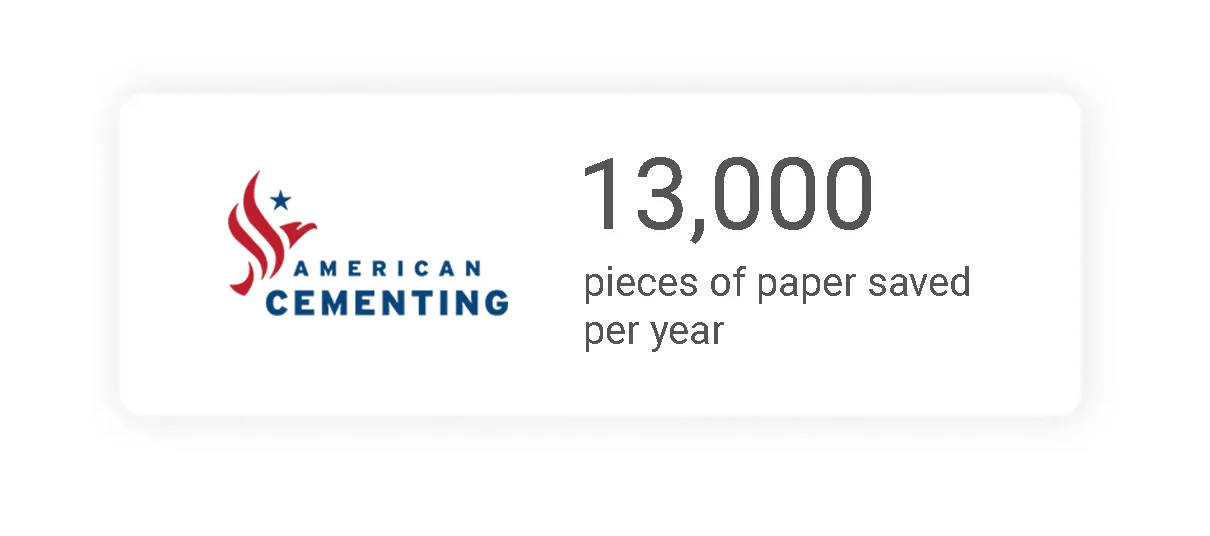
Meet American Cementing
Administrative paperwork was manual and inefficient
American Cementing is a leader in cementing services for the oil and gas industry. Handling cement is time-sensitive—American Cementing needed to have a seamless connection between the field and back-office so that technicians can work fast, but that’s exactly where they faced challenges. Prior to operating heavy equipment at well sites, field technicians would need to deal with piles of paper-based documents, such as pre-inspection reports and fuel receipts, opening up the possibility of human error and inefficiency. This would trickle into the back-office, with the administrative team needing to manage the resulting paperwork manually.
American Cementing’s back-office team was also overwhelmed by time-consuming payroll processes. Before Samsara, driver logs and the internal payroll software lived in separate places, meaning the administrative team would need to painstakingly compare records, day by day, every pay period. Issues with payroll were only made worse when drivers forgot to log off once they’re off duty, leading to inaccurate payments and a lowered employee experience.
TRAVIS WEISHAAR
Digitized documents and system integrations streamlined fuel management and payroll
American Cementing installed 400+ Vehicle Gateways across their fleet and introduced the Samsara Driver App to their field technicians. Using Documents in the Driver App, both the frontline and back-office teams were able to go completely paperless.
American Cementing created customized DVIRs with specific fields for function tests to make pre-job equipment inspection reports as efficient as possible. And by integrating Samsara Documents with data from their fuel payment provider FLEETCOR Comdata they were able to eliminate weeks of processing time and streamline fuel management. Instead of stuffing weeks’ worth of mangled fuel receipts into envelopes and mailing them to remote locations for filing, technicians can simply scan their receipts with their mobile device and enter in a few key details to instantly share their fuel receipts with the back office. This ensures accurate fuel purchase tracking and tax compliance.
The team at American Cementing also integrated their internal payroll software with Samsara to automate payroll processes and improve the employee experience. The administrative team no longer needed to manually cross-reference hours of service data, since it would automatically flow between Samsara and their payroll provider via open API. The back-office team can also now remotely sign out drivers from the Driver App, significantly improving the accuracy of driver hours and payroll.
The back-office team was able to save over $60,000 per year
American Cementing was able to realize tremendous efficiency improvements in the field and back office as a result of Samsara. By using the Samsara Driver App, American Cementing was able to transition from paper and digitize key documents, saving around 13,000 pieces of paper yearly.
Samsara’s easy-to-use, turnkey integration with FLEETCOR helped improve productivity and time-savings, leading to around $60,000 saved per year in labor, shipping, and fuel costs. In addition, American Cementing’s custom integration with their payroll software saved their back office over 1,600 hours per year —and was set up in just 1.5 weeks.
As a company focused on innovation, American Cementing was able to enhance the experience for workers in the frontline and the back-office by adopting Samsara. “Learning new systems and adapting to new technology is stressful not only for employees in the field but also for employees in the back office,” said Travis Weishaar, EHS and DOT Manager. “We chose Samsara for its simplicity, ease of use, and advanced technology. And by integrating it with other systems, we were able to reduce stress, save time, and definitely increase productivity.”